Warehouse Inspections
Warehouse Inspections
Regardless of the warehouse size, regularly scheduled inspections are vital for ensuring the safety of employees, the integrity of products, and the overall efficiency of operations. Storage solutions such as racks and shelving systems support a wide range of products, often packaged in varying sizes. Therefore, it is essential to verify that these systems remain stable and secure to prevent accidents and maintain a smooth workflow.
Neglecting inspections can have serious consequences that disrupt warehouse operations. Missing these critical evaluations can lead to injuries, property damage, and violations of safety regulations, which may result in significant financial losses. Companies risk not only losing profits but also facing a decline in employee morale and trust, which can tarnish their reputation in the industry.
Furthermore, inadequate oversight can lead to increased insurance premiums and potential legal liabilities, as safety violations often attract scrutiny from regulatory bodies. An unsafe work environment not only heightens the risk of accidents but can also contribute to higher employee turnover rates as workers seek safer job conditions elsewhere.
In short, regular inspections are not merely a regulatory requirement; they are an essential component of a safety strategy that protects both employees and assets within the warehouse. Warehouse managers are liable for keeping all persons within the facility safe, so these inspections will ensure that safety is paramount.
Benefits of Regular Inspections
Warehouse inspections lead companies to success as this service verifies that the warehouse is a safe and workable environment. Inspections benefit the following aspects: safety, efficiency, compliance, and cost savings. Notably, employees are ensured that their safety is at the forefront of a company policy and they are protected from injuries.
Safety
One of the primary advantages of conducting regular inspections is enhancing safety. By identifying and addressing potential hazards—such as improperly stored items, damaged equipment, or obstructed pathways—inspections help prevent accidents. A proactive approach to safety not only protects employees but also fosters a culture of well-being within the workplace.
Moreover, reducing the risk of accidents contributes to higher profitability. When safety is prioritized, orders can be fulfilled promptly and efficiently, minimizing disruptions. Additionally, with fewer injuries, there’s a reduced risk of employees being unable to work, further supporting the overall productivity and success of the operation.
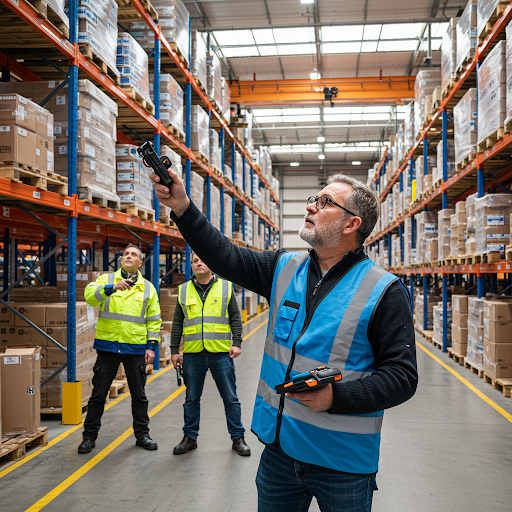
Efficiency
Efficiency is critical to the smooth operation of any warehouse. Regular inspections ensure that storage systems and retrieval processes are optimized. By evaluating the layout and organization of products, companies can streamline operations, reduce retrieval times, and improve overall productivity. This attention to detail helps create a more effective workflow, allowing employees to focus on tasks without unnecessary delays.
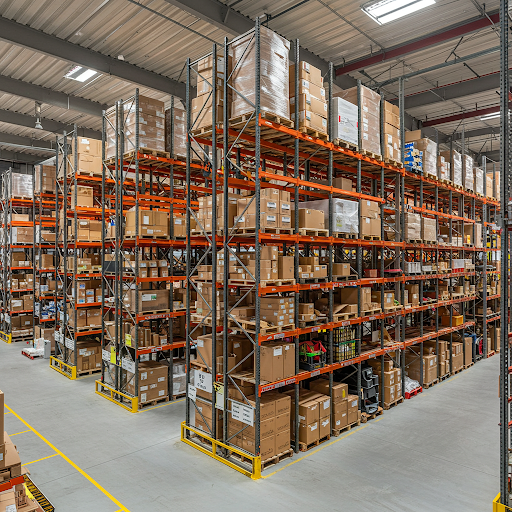
Compliance
Adhering to industry standards and regulations is essential for any business. Inspections help ensure compliance with safety protocols, environmental regulations, and industry-specific guidelines. By regularly reviewing these standards, companies can avoid penalties and fines while maintaining a good reputation in the industry. Compliance also demonstrates a commitment to quality and safety, which can enhance employee trust.
Cost Savings
Regular inspections can lead to significant cost savings in the long run. Companies can prevent costly repairs and equipment replacements by identifying issues such as equipment malfunctions or structural storage problems before they escalate. Investing time in inspections helps ensure that resources are used efficiently and that the warehouse operates smoothly, ultimately contributing to the bottom line.
In conclusion, regular inspections are an essential practice for warehouses, providing numerous benefits that enhance safety, efficiency, compliance, and cost-effectiveness. By prioritizing these evaluations, companies position themselves for success in an increasingly competitive marketplace.
Key Inspection Areas
USSI inspectors will walk through the warehouse and review key areas that need to be thoroughly inspected and noted. The evaluation will look at these key components: rack structures, storage systems, and forklift traffic. While examining all critical areas of the facility, our inspectors will take notes to provide reports and recommendations at the end of the visit. Reports will be detailed and specific to what improvements need to be made to adhere to industry standards.
Rack structures are in essential part of the warehouse and must be adequately maintained in order to keep them in tip-top condition but also safe for those working in the warehouse. When checking the rack structures, inspectors will follow a checklist to mark whether or not it passes or needs to be addressed. This checklist typically includes criteria such as:
- Structural Integrity: This factor will determine whether there are any cracks, bends, or corrosion on the racks. If so, they will need to be fixed or even replaced. The structure of the shelves and racks hold products of all sizes and weights. Therefore, warehouses need to make sure they stay within the weight capacity of the shelving units.
- Load capacity and compliance: Verifying that the racks are not overloaded and that load limits are clearly marked and adhered to. Given the immense volume of boxes and packages placed on these racks, proper maintenance is essential to reduce the risk of accidents and extend the lifespan of the shelves.
- Proper anchoring and bracing: Due to the high traffic these rack structures experience—constantly moving products, adding new boxes to the shelves, and rearranging the layout—secure anchoring is critical to prevent the shelves from shifting or toppling. Regular inspections should ensure that anchors and braces are intact and functioning properly. This stability not only protects the integrity of the racks but also safeguards employees from potential hazards associated with unstable shelving.
Storage systems are another critical component for inspections. While not every item within the warehouse can be added to the racks due to weight capacities, those items must be properly stored and stacked in areas not high foot traffic. Practicing storage systems will lead to organization, proper pick module solutions, and compliance with industry standards.
While inspectors walk through warehouses and inspect the shelving units, they look at the condition of the shelves, pallets, and other storage solutions. Whether that’s an additional storage area in the back or in an office area, inspectors are likely to check the space to ensure it’s safe. The reason is that inspectors must confirm that all products within storage areas are adequately stacked. Being able to maneuver through the storage areas is crucial to employee safety and being able to access the products easily, especially for those utilizing equipment.
Load capacities are a crucial factor for inspectors to consider when evaluating shelving units. They must assess whether the units are operating within their weight limits and if additional space exists for storing more products. Inspectors will document their observations and include recommendations in their reports regardless of their findings. Shelves and pallets must stay within their weight limits, as overloading can lead to bending, breakage, and damaged products.
Warehouse equipment used to move products throughout the facility requires regular inspection. Ensuring that this equipment is functioning properly, kept clean, stored correctly, and operated exclusively by authorized employees is crucial. Proper maintenance of forklifts ensures operators’ safety and reduces the risk of injuries and accidents. Operators must be well-versed in the latest safety procedures and regulations.
USSI inspectors play a key role in this process, as they verify that all forklift operators use the equipment correctly and are aware of their surroundings. They also assess whether there is sufficient space for safe navigation within the warehouse, considering factors such as aisle width and clear pathways. By prioritizing these inspections and training, warehouses can foster a safer working environment and enhance overall efficiency.
Inspection Checklist and Documentation
After the inspection, USSI employees will provide warehouse managers with a detailed report outlining their findings, recommendations, and suggestions for improvement. This report will include a comprehensive checklist that managers can review to implement necessary changes and ensure compliance with industry standards.
Additionally, inspectors will analyze past inspection reports to identify trends and patterns in previous results. This historical data will help USSI employees assess ongoing issues and track improvements over time, enabling warehouse managers to make informed decisions about enhancements to their operations.
For companies seeking a thorough and professional warehouse inspection, contact USSI today. Trust us to deliver a detailed report that keeps your warehouse safe and ensures compliance with industry standards. With our expertise, you can foster a safer and more efficient work environment, ultimately supporting your business’s success.